Structural Analysis and Design Optimization: Theory and Practice
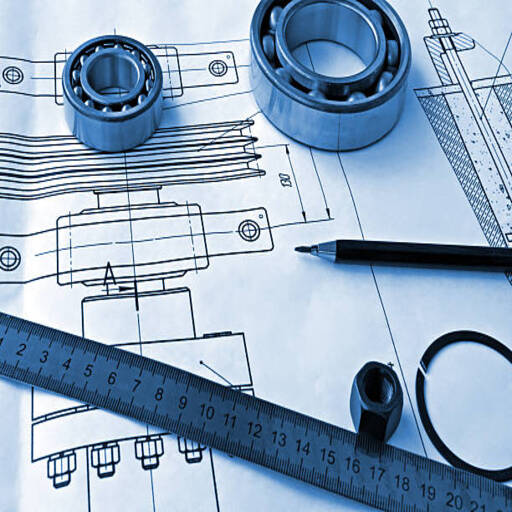
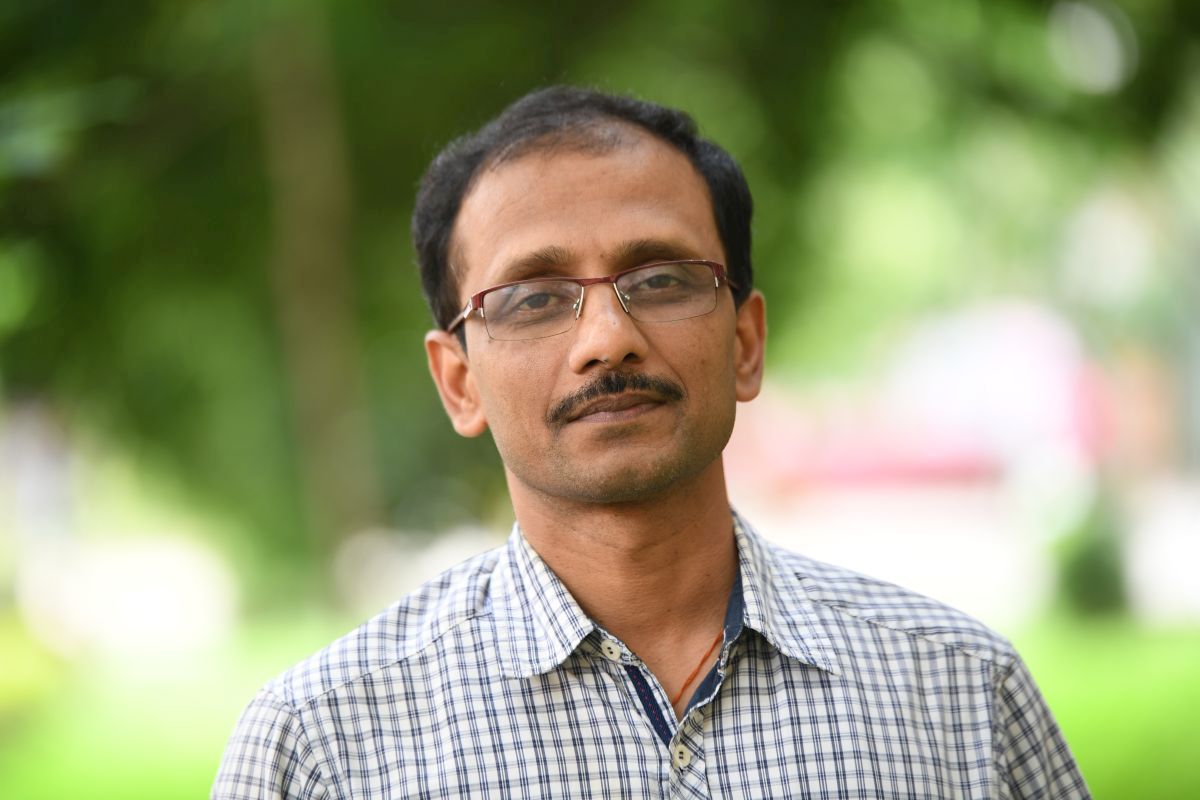
Dr. S B Kandagal
Principal Research Scientist,
Department of Aerospace Engineering
Objective
Advanced research in material science to enhance life with reduced cost resulted in metal alloys, plastics, composites and nano materials. Structural design and optimization of components with unusual shapes became possible with current available finite element software tools such as ANSYS, NISA, NASTRON, ABACUS, SYSNOISE, LSDYNA and MATLAB etc. The fundamental knowledge of stress, strain, shear, torsion in relation to the structures and S-N curves in relation to the material fatigue life becomes important. The interpretation of the FEM software output calls for the knowledge of analysis and design optimization of mechanical systems. This course essentially trains engineers/scientists/entrepreneurs/instructors in the industries/institutes to optimally design various mechanical systems and sub-systems for technically superior and commercially viable value-added products and achieve “EMPOWER INDIA WITH SKILL AND Knowledge.”
Syllabus
Applied mechanics, Strength of materials, SFD, BMD, AFD, solid mechanics, concept of stress, strain and fatigue. Constitutive laws. Mohr’s Circle, Engineering materials and their properties. Structural analysis concepts, tension, compression, shear, torsion, coupled system, and S-N curves. Design of beams, torsion, compression members and fasteners. Stability of structures. Composite materials and their importance in structural analysis design optimization. Principles of optimization, formulation of objective function and design constraints, classification of the optimization problem. Single and multivariable optimization. Optimization with equality and inequality constraints. Optimal design of mechanical elements – fasteners, springs, gears, bearings, belts, clutches, brakes, shafts, and axles. Procedures for product design, development and testing. The vibration of structures Practical problem discussion with industrial products (optimization of passenger car subsystems for vibration and noise reduction, Rail-coach-CBC couplers, Car door window regulator, satellite tracking antenna and DWR antenna design, Tractor canopy, hydraulic crawler driller (drilling machine), Bike brake system, sluice valve design, failure analysis if piston drill bit, thermally insulated box, IP turbine blade failure analysis, design analysis of super pump impeller, Structural design aspects in power plants. Hydraulic jacks/Feed cylinder with intermediate supports, Industrial chimney design, optimization of box culverts, metal-composite sprocket for bikes, Thermal analysis of heat exchangers, 6- DOF force balance, pitch flexure, roll flexure design for wind tunnel model studies for aerodynamic derivatives of aerospace vehicle and automobiles).
|
Target AudienceMechanical, Civil, Aerospace, Automotive, Industrial engineers, R & D Labs, Construction technologists, new product design and development groups, Entrepreneurs and Engineering college instructors. Professionals to pursue postgraduate and higher studies. |
|
Eligibility criteriaBE, ME, MSc, AMIE, or equivalent
|
![]() |
Course Fee₹ 10000 (Excluding 18% GST) |
|
Number of Credits2:0
|
![]() |
Mode of InstructionOnline with Synchronous mode
|
|
Duration5 Months( Aug – Dec 2024) |
|
Timings of the classSaturday (12.00PM to 2.00PM).
|